June 10, 2025 The photography exhibition titled “Saline di Volterra, a Presidential Inauguration (1959)” was…
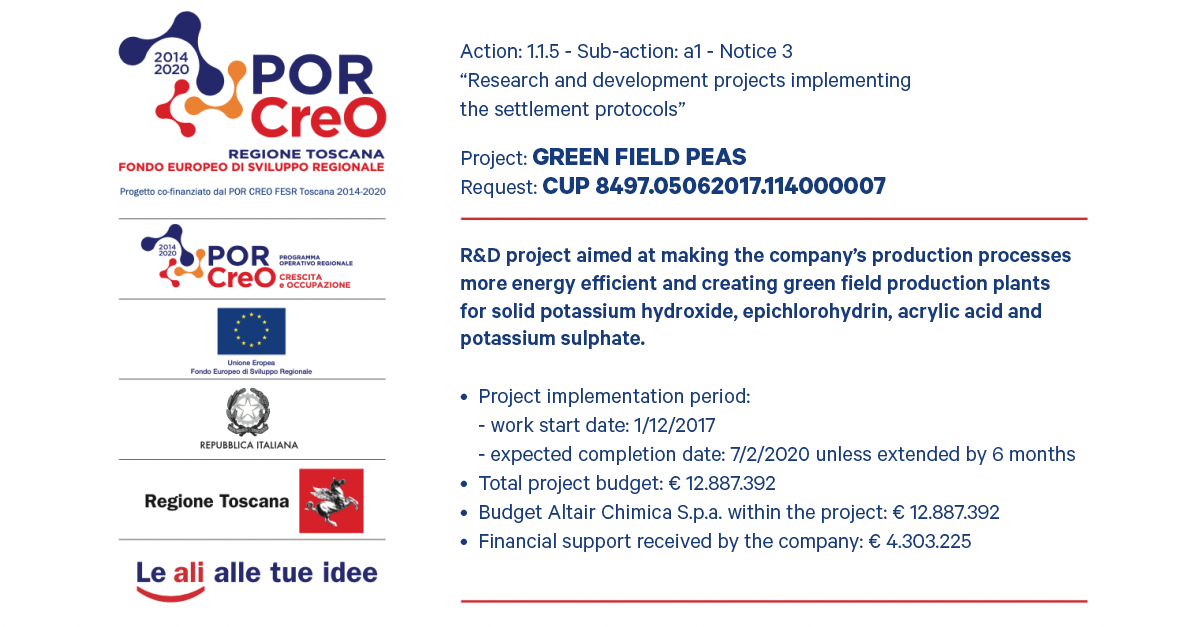
On August 4, 2017, ALTAIR CHIMICA submitted a grant application as part of the Tuscany Region’s call for Research and Development Projects (within the Regional Operational Programme for Growth and Employment) and the European Union (through the European Regional Development Fund) for the G.R.E.E.N. FIELD PEAS project. This is an R&D project aimed at energy efficiency of corporate production processes and the establishment of greenfield production plants for solid potassium hydroxide, epichlorohydrin, acrylic acid, and potassium sulfate. Initiated by Altair Chimica on December 1, 2017, the project was granted funding on February 7, 2018.
The G.R.E.E.N. FIELD PEAS project, under POR CreO FESR Toscana 2014/2020 Action 1.1.5 – Sub Action a1 – “Research and development projects implementing Settlement Protocols” (Call 3), consists of 7 project lines or sub-projects:
- R&D of Innovative Technologies aimed at significant CO2 and heat recovery in the production process of potassium carbonate, intended to reuse the outgoing CO2 from the cogenerator to produce K2CO3.
- R&D of the technical and operational characteristics of an innovative bi-fuel methane-hydrogen burner.
- R&D of an innovative plant, from greenfield, for the production of epichlorohydrin, starting from feedstock present in Altair Chimica or easily obtainable in a short supply chain, from bio-fuels by-products.
- R&D of an integrated management system and optimization of the production and consumption processes of hydrogen and chlorine following the start-up of the new caustic soda production plant – SODA-4.0 Project (Automated Decision and Optimization System 4.0).
- R&D of an innovative potassium sulfate production plant.
- R&D of an innovative solid potassium hydroxide production plant, starting from the 50% aqueous solution already present in the plant.
- R&D of a self-production plant for electrical energy from renewable (geothermal or hydroelectric) or low environmental impact fossil sources, with very high efficiency (natural gas co-generation).
The total budget for the project, expected to conclude in 2020, is €12,887,392; financial support granted to Altair Chimica is €4,303,225.
Specifically, for the SODA-4.0 Project, the goal is to develop and implement an integrated management system and optimization of the production and consumption processes of hydrogen and chlorine following the new production layout of Altair, which was realized with the start-up of the new NaOH (caustic soda) production plant. In summary, it consists of creating a robotic/automated system capable of interfacing all the information present in the DCS (Distributed Control System) and in the company management system and making optimal decisions in terms of productivity, energy consumption, and performing operations with the highest degree of safety possible, always performing perfectly coded operations, without human errors and/or various oversights.
Specifically, the optimization system will take as input the requested production of KOH, K2CO3, solid KOH, NaOH, and chlorinated products, as well as the energy cost of the various hours in which the productions will take place (PUN, National Unit Energy Price) and must provide, in real-time (Real-Time Optimization), the modulation of the operation of the chlorine-producing plants (electrolytic cells) and chlorine-using plants (chloroparaffins, sodium hypochlorite, technical ferric chloride, potable quality ferrous and ferric chloride, and hydrochloric acid), to output everything necessary for the execution of customer orders at the lowest possible energy cost within the required production period. The acquisition of all necessary data, both from the DCS for production data, from the AS400 (commercial data), and Energy (web platform on the GSE’s PUN), will occur through the use of a snap4city platform, which must be capable of receiving, via a dynamic connection specifically developed between DCS, web, and AS400 management system, all data coming from the plant through the instrumentation interfaced with the DCS and with all data coming from AS400, such as customer orders and with the energy information needed to optimize energy costs. An additional connection may also be planned that allows the AS400 management system to automatically receive customer orders, avoiding the current phase of manual entry of the same. This possibility will be foreseen in the development of algorithms and various routines to be developed, but will require the assistance of customers willing to such development, therefore it will be articulated later after the release of this project.
The platform will acquire input data from the DCS and provide its outputs to the DCS itself, through the routines developed in the RTO; therefore, the optimization system will occupy a hierarchically superior layer to the DCS and will thus operate as an “automatic operator.”
The RTO system will calculate the operating configuration of the chlorine-producing and consuming plants through the resolution of a constrained optimization problem over an appropriate temporal horizon, taking into account material and energy balance models of the plants, minimum and maximum operating constraints of the plants, available storage in the plant, hourly energy costs, and interlocks already present on the plants in terms of process and safety.
The system can operate in two modes:
- Background mode (decision support): the RTO system, once the data is acquired, processes the optimal operating configurations of the plants and proposes them to the operator, who will then decide which configuration values to use; the proposed values are still historized by the DCS;
- Online mode (automatic decision): the RTO system, once the data is acquired, processes the optimal operating configurations of the plants and “writes” them in real-time on the DCS, thus operating automatically on process and production control.
The background mode will be used in an initial commissioning phase to validate the correct functioning of the RTO system and to identify necessary changes and improvements. Once deemed reliable, the system will be switched to online mode for a further validation and refinement period, eventually obtaining the definitive RTO system, which will operate automatically. Obviously, the operator can switch from online mode to background mode and vice versa at any time, thus ensuring the perfect resilience of the control system in the face of possible malfunctions.
From the moment the RTO system becomes operational, the platform will implement all the logic and routines necessary for the production of statistics and analysis of the big data that will be continuously recorded by the plant and the management system, so as to have all the input data available to provide to self-learning algorithms, to automatically feed the overall performance improvement of the 4.0 system, through new or better commands to be returned both to the DCS and to AS400.
Innovative Aspects of this Project
At present, there are no chlor-alkali or chlor-potash plants that go beyond the presence of a control room with a DCS, more or less complete in terms of interfaced instrumentation. To date, the maximum level of automation stops at this level, in which the presence of the control room technician and the presence of external operators, ready to act based on the operations necessary for regulating the various productions, is expected. Today, wherever a chlor-alkali or a chlor-potash is located in the world, decisions on the production configurations of the various departments are decided by more or less complex management systems, which transfer their output to the various production planning managers, who, in turn, mediating between commercial and production needs, establish which information to send to the control room technician, who, finally, will give his men and the DCS the instructions to drive production in the decided direction.
Such inputs have two orders of problems: they suffer from potential human errors of judgment, potential oversights in some elements of the decision chain, and the possibility of error in performing all the maneuvers necessary to run the entire plant according to theoretical desires.