In anticipation of the corporate merger that took place at the beginning of January, Altair…
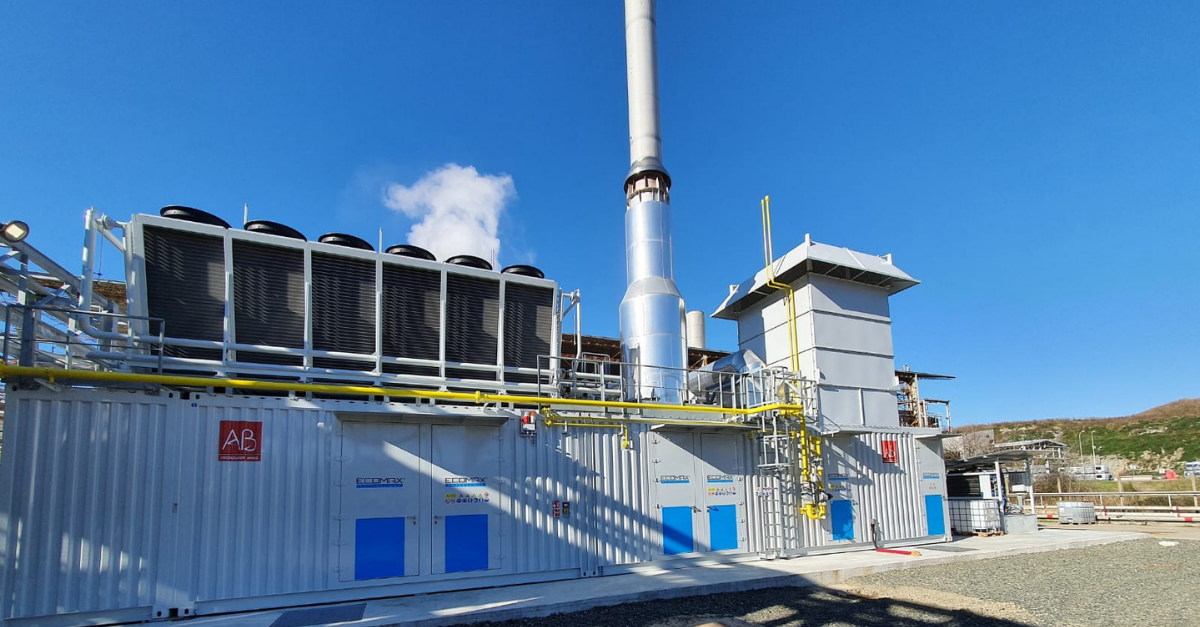
A new cogeneration power plant was inaugurated in Saline di Volterra with a capacity of over 2,000 kWe: it will help cover the needs of the plant which, in the meantime, has significantly increased its output.
One of the key objectives in the strategy of the Chloro-Alkali Division at the Esseco Group, that includes Altair Chimica, Altair Iberica and Hydrochem, is sustaining constant growth through focused investments that involve innovation, efficiency and sustainability.
The consistent growth recorded in recent years thanks to the development of new processes and products and upgrading existing plants, among other things, has led to an increase in the power supply demand at the Saline plant: to address this rise, new solutions were sought for energy self-production, which led to the addition of a brand new high-efficiency cogeneration plant to the existing gas turbine cogeneration plant: the investment costs approximately 2 million Euros with a saving which predicts a paybackin just 3 years.
The new plant, based on an internal combustion engine fuelled by natural gas, features electric power generation at full load of 2,006 kWe and a thermal energy recovery system, which will produce an overall efficiency of more than 86%.
A computerised platform continuously monitors each element and parameter of the system, ensuring excellent performance and maximum safety at all times and under all operating conditions.
Cogeneration is globally recognised as one of the best technological applications to ensure energy efficiency and subsequent environmental sustainability, thanks to the combined production of electricity and heat, which, by itself, guarantees significant energy savings compared to separate productions.
Why is cogeneration at Altair an efficient and sustainable system, even though it starts from methane gas (which is not a renewable resource), that generates CO2 during combustion and is harmful to the environment?
Its efficiency lies in the fact that, more than 50% of the electricity purchased from the network is generated by thermoelectric power plants, wasting a great deal of thermal combustion energy (the average efficiency is 55% in Italy; as a result, 45% of the fuel we burn is wasted), with no on-site thermal consumption capable of absorbing this heat. Our cogenerators perform at over 85% because they are designed to generate hot water and steam used by the plant in its production process. They have been designed to meet our needs, without waste. So they are highly efficient.
Sustainability, on the other hand, comes from Altair recovering the CO2 from the methane gas combustion and producing potassium carbonate, without emitting it into the atmosphere.
As far as the emission of pollutants into the atmosphere is concerned, the new Saline plant can boast:
– a patented system of emissions control;
– partial use of the combustion fumes in a new plant to produce solid potassium carbonate;
– an innovative reuse technology for CO2, preventing it from being released into the atmosphere.
High efficiency operations (CAR-High Efficiency Cogeneration, when it exceeds 70%), make the plant eligible for receiving white certificates (called TEE – Energy Efficiency Certificates), by the GSE (Energy Services Manager, the body assigned by the Italian State to pursue and achieve environmental sustainability objectives, in the two pillars of renewable resources and energy efficiency). These are negotiable certificates that certify the energy savings achieved thanks to work carried out to increase efficiency. For each TOE (Tonne of Oil Equivalent) of savings achieved thanks to the implementation of energy efficiency initiatives, a certificate is awarded for 10 years. In the case of Altair’s second cogenerator in Saline di Volterra, it is estimated that about 2,000 white certificates will be received per year.